Unite quality and production to hit goals every shift.
DIGITAL PLANT MANAGEMENT
Unite Production & Quality to Improve Plant Visibility, Control, and Performance
Change. For Good.
How Good?
• $20 million in waste savings from a global quality system • 35% production gain in two weeks from tracking and trending data in real time • 20% more throughput and eliminating a hard-to-fill weekend shift.
Maximize throughput and yield
With data-driven insights placed in the hands of frontline workers, operators take decisive action to optimize production runs.
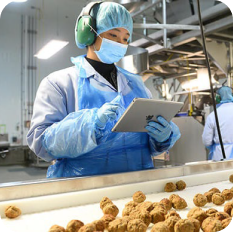
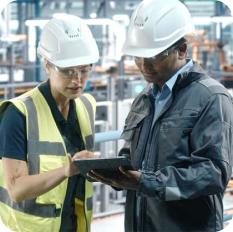
Ensure quality and compliance
Minimize costs of poor quality and waste, while reducing incidents through defined processes and audit-ready documentation for quality, EHS, and supplier performance.
Optimize labor and productivity
Empower operators with data visibility, automated tools, and reporting to build a culture of collaboration, accountability, and labor efficiency.
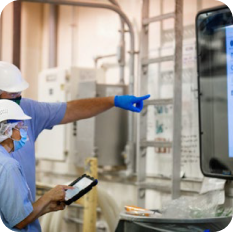
Improve plant-wide performance with digital plant management
Address Plant-Wide Challenges, as a Team
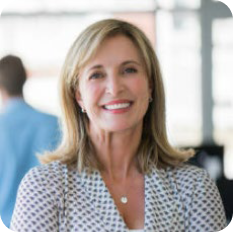
COO
• Struggle hitting performance targets
• Production delays & overtime costs due to downtime, delayed line starts, & line changeovers
• Customer complaints due to shipping delays or poor product quality
• Limited visibility into shop floor activity due to lack of data
• Silos between departments and systems
Plant Manager
• Tight operating margins & pressure to reduce costs
• High employee turnover & shortage of skilled workers
• Fluctuations in demand & supply chain issues
• Inconsistent or poor product quality
• Orders not shipped on-time
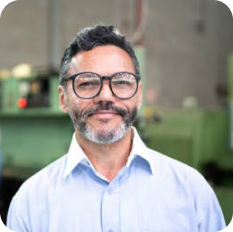
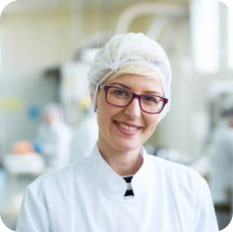
FSQA Director
• Struggle hitting performance targets
• Managing suppliers
• Customer complaints due to shipping delays or poor product quality
• High costs due to waste and scrap
• Keeping up with regulatory and compliance changes
Digital Plant Management
Trusted in Thousands of Facilities
SafetyChain gives process manufacturers the flexibility to rapidly address urgent challenges while offering scalability to expand and drive long-term value.
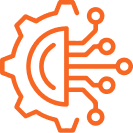
Capture All Critical Data
Digitally capture and unify data from multiple sources, including operators, machines, and sensors.
• Gain real-time visibility into what is happening throughout the facility • Eliminate organizational silos made worse by competing data sources • Feel confident your teams are relying on consistently accurate data
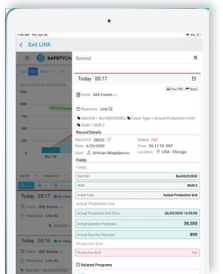
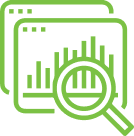
Gain Plant-Wide Insight
Visualize data with role-based dashboards and conduct real-time and historical analysis.
• Know at-a-glance whether you’re hitting your metrics
• Pinpoint areas of improvement to reduce waste, increase yield, and maximize throughput
• Better understand how your teams are performing to create labor efficiencies
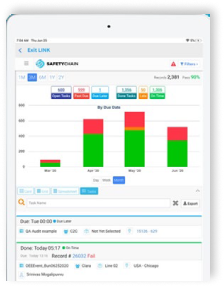
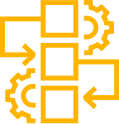
Take Rapid Action
Drive plant-wide processes, track compliance, and prepare for audits with programmatic documentation and role-based automated workflows.
• Save time and ensure you’re always audit-ready
• Eliminate guesswork so everyone knows what they need to do and when
• Increase efficiency and foster a culture of problem-solving
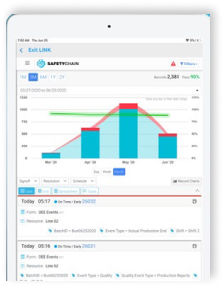
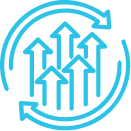
Plan Scalable Growth
Create an achievable adoption plan with support from our hands-on coaching team
• Drive change, not disruption, throughout your plants • Ensure the short-term and long-term success of your implementation • Justify current and future technology investments by reducing waste and increasing productivity
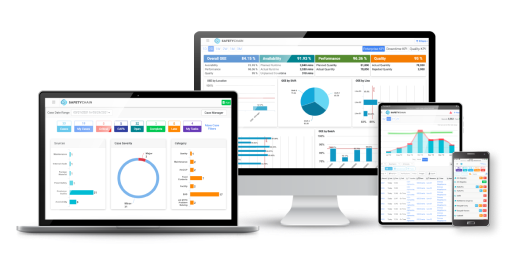
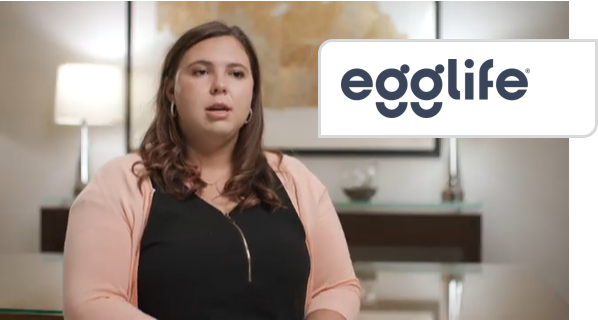
Egglife Foods: Aligning Production and Quality with a Plant Management Solution
EggLife Foods talks about how access to real-time data has helped align quality and production across the plant and future plans to implement SafetyChain in other areas of its operations.
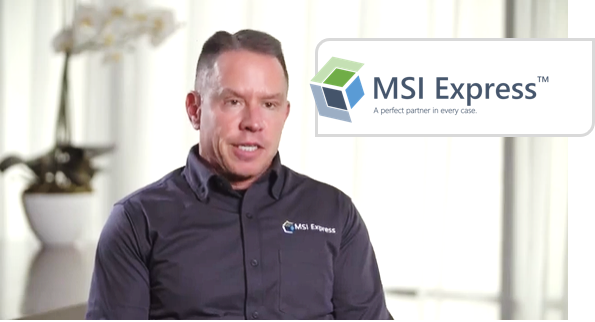
MSI Express: Data Driven Quality Operations with SafetyChains Plant Management Platform
Craig Verhoff, Chief Quality Officer at MSI Express explains how they connected the dots across production and quality to understand the full picture with real-time data with SafetyChain. By digitizing…
Who is using SafetyChain?
Read success stories from some of the process manufacturing industry’s most well-known names
See how SafetyChain Software unites quality and production operations